CVTANK
Military Grade, Closed Volume Hydraulic Tanks for Mobility Systems
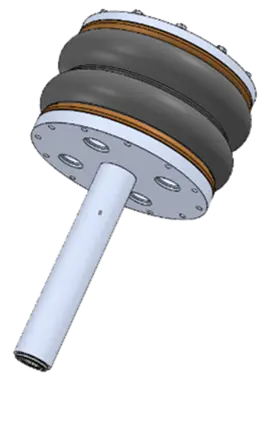
CVTANK helps any hydraulic circut to transform into a closed circuit hydraulic system and it stores precisely the required volume of oil needed to operate the hydraulic system.
Acts as a low-pressure accumulator with much more pressure precision and reliability to keep suction pressurized all times.
Pumps have pressurized inlets to work at their max flow capacity.
Eliminates welded tank designs, breathers, unreliable oil level sensors, sight gauges, sloshing analysis, foaming, cavitation due to dry leakage lines.
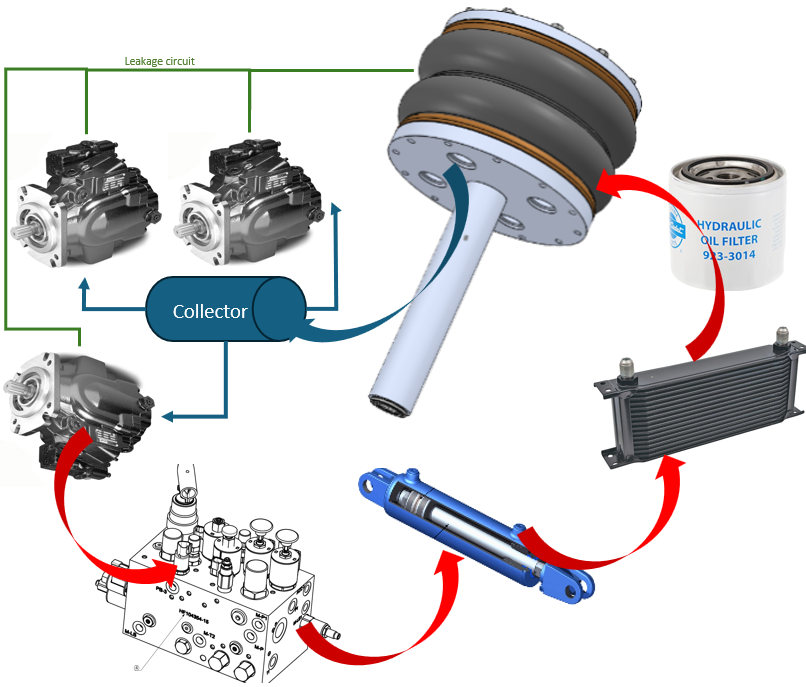
Tighten the powerpack
CVTANK Can be installed at any place near a return line.
Reduces total hydraulic fill volume down to 30 liters for a typical 8x8 defense vehicle application having 250 liters.
CVTANK can be integrated on powerpack and it can be serviced with powerpack.
A Powerpack integrated with a CVTANK can be run on shopfloor without having any additional hydraulic source.
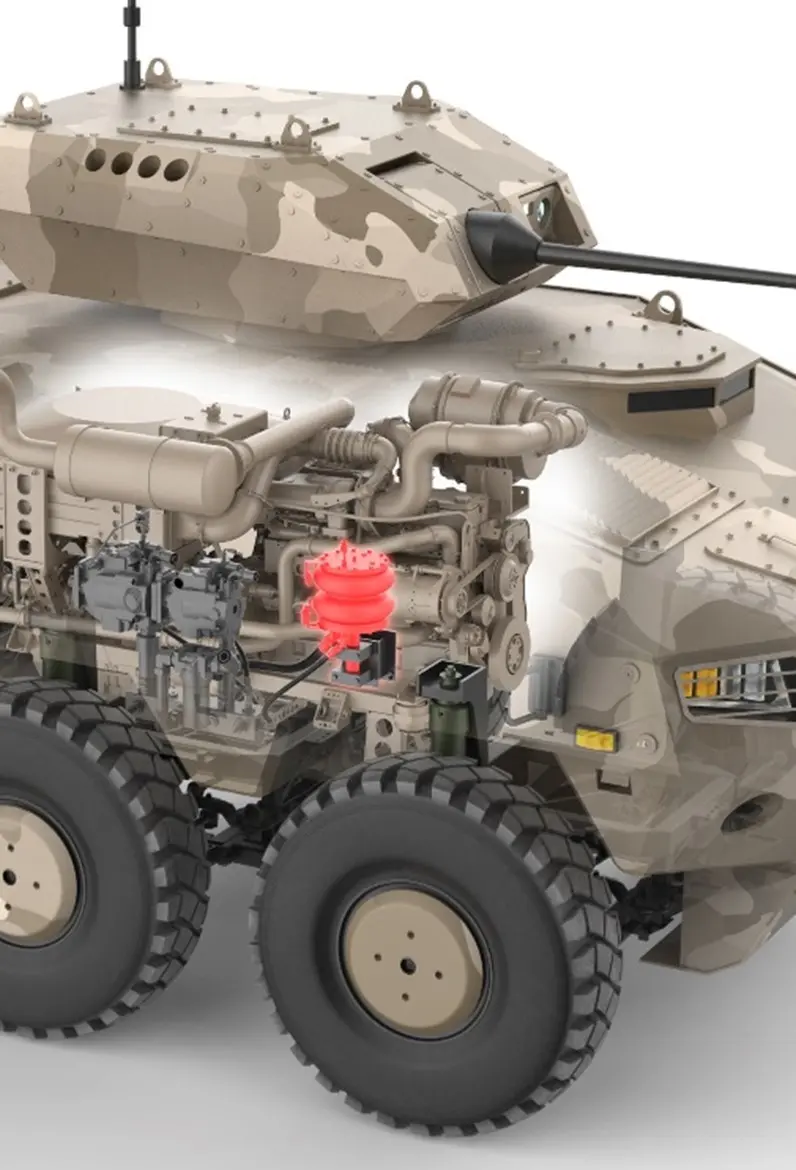
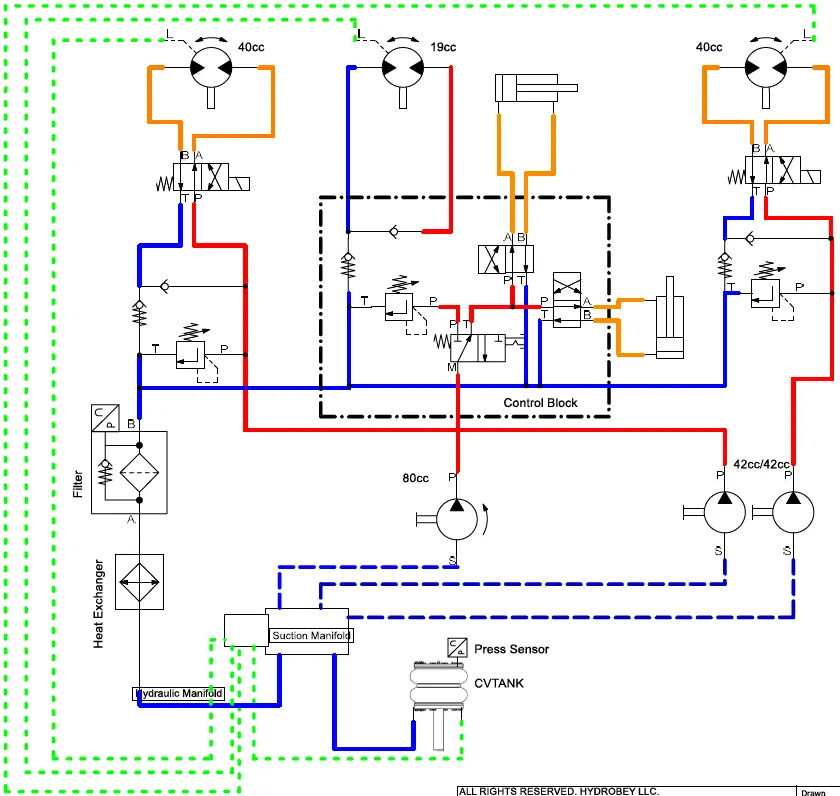
Proven performance
20 years of hydraulic design experience for defense land vehicles and railway systems.
8 different defense vehicle platforms 8x8, 4x4, 6x6, tracked and locomotives.
Combat proven on tropical and desert conditions.
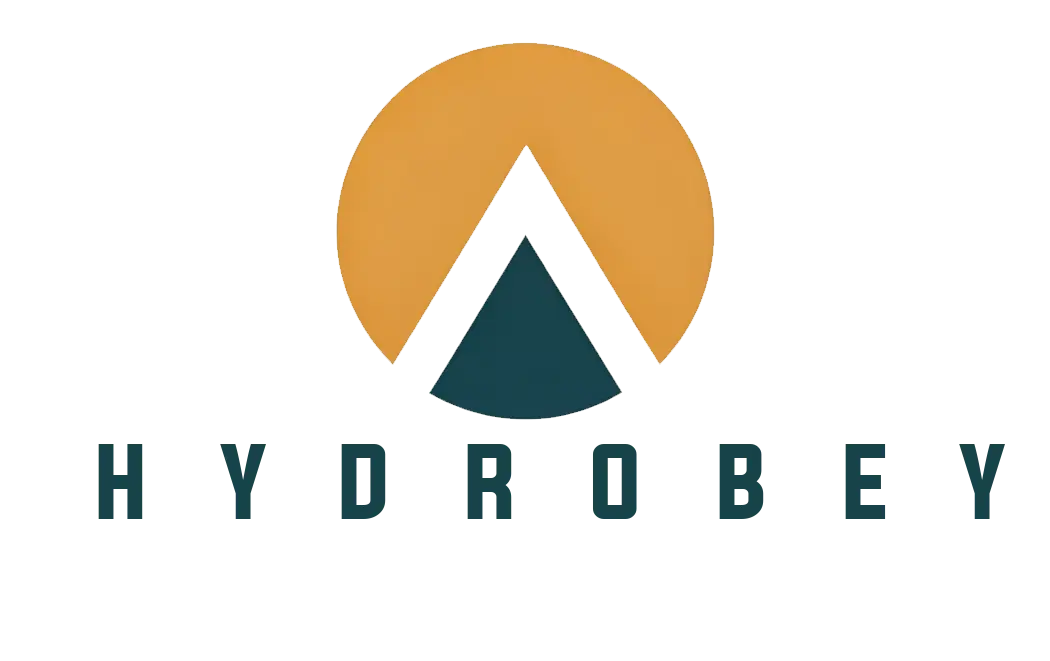
CVTANK-2.7
Empty Weight (lbs) | 15 |
Max Allowable Volume expansion (lt) | 2.5 |
Working Pressure (bar) | 0.8 |
Ambient Temperature | -40°C - 100°C |
Max Allowable oil Temp | -30°C - 90°C |
Burst Pressure (bar) | 16 |
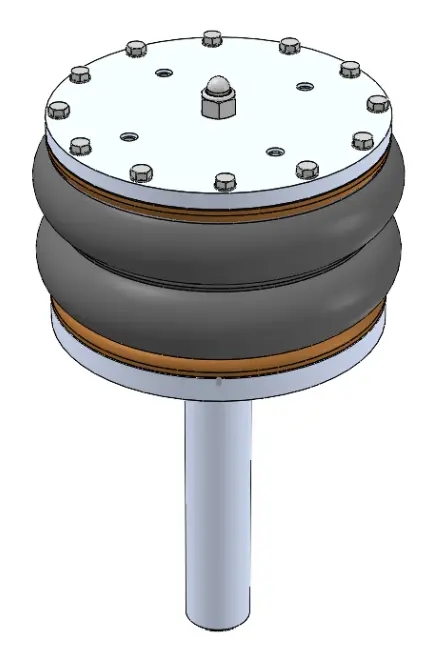
CVTANK-6.7
Empty Weight (lbs) | 35 |
Max Allowable Volume expansion (lt) | 6.7 |
Working Pressure (bar) | 0.8 |
Ambient Temperature | -40°C - 100°C |
Max Allowable oil Temp | -30°C - 90°C |
Burst Pressure (bar) | 16 |
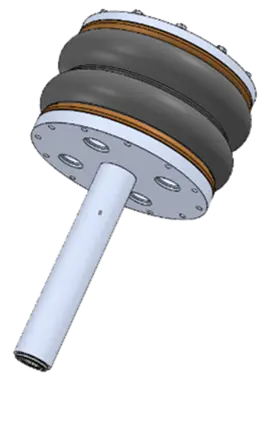
CVTANK-4.6HP
Empty Weight (lbs) | 35 |
Max Allowable Volume expansion (lt) | 4.5 |
Working Pressure (bar) | 2.5 |
Ambient Temperature | -40°C - 100°C |
Max Allowable oil Temp | -30°C - 90°C |
Burst Pressure (bar) | 16 |
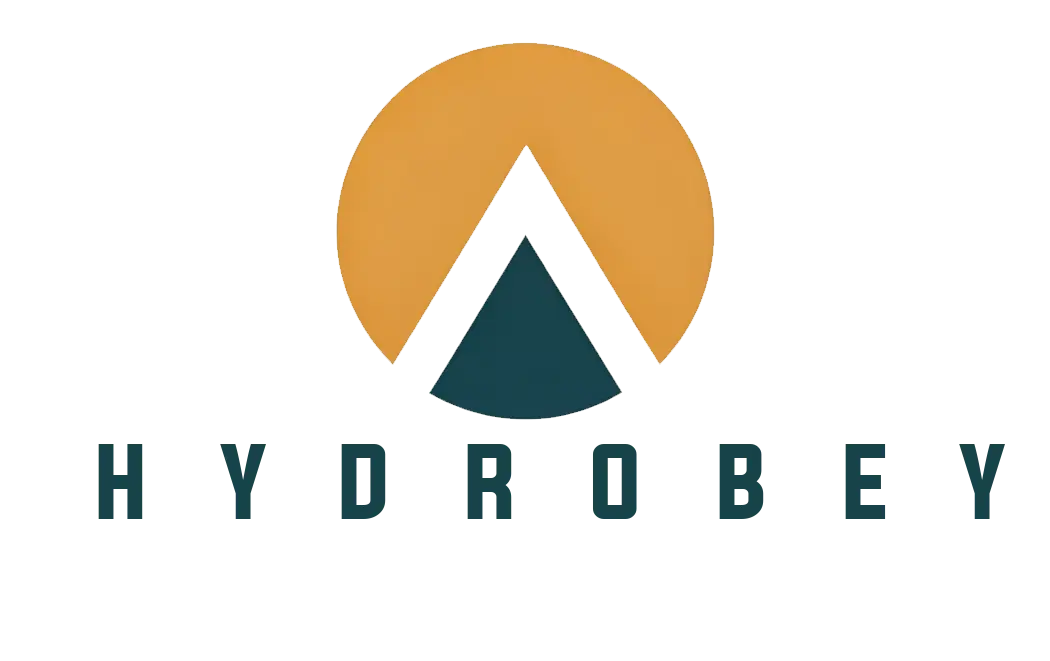
CVTANK-15
Empty Weight (lbs) | 40 |
Max Allowable Volume expansion (lt) | 15 |
Working Pressure (bar) | 1.15 |
Ambient Temperature | -40°C - 100°C |
Max Allowable oil Temp | -30°C - 90°C |
Burst Pressure (bar) | 16 |
What is CVTANK?
CVTANK, stores only necessary amount of oil required
I In hydraulic systems, hydraulic oil circulates between tank, pumps and actuators. The volume of oil in circulation remains constant unless an actuator requires a volume adjustment, such as during cylinder actuation or accumulator charge/discharge. Additional parameters that exert a lesser influence on circulating oil volume include fluctuating pump volume, thermal impacts, and hose flexing resulting from pressure. The primary function of the tank is to accommodate the max amount of oil required at any given moment, considering these combined criteria.
in a traditional tank it is impossible to store only this exact amount of oil to be able to supply the system. In these tanks, returning hydraulic oil brings air pockets inside it. In order avoid cavitation effects, this suspended air should be got ridden off from the oil before a pump sucks it.
Consequently, a standard industry practice is to design a hydraulic tank that accommodates at least three times the maximum attainable flow inside the system. Nevertheless, with mobile machinery, this design principle is overlooked due to the characteristics of the platform. Design authorities mitigate the deterioration risk of components or employ advanced tank design techniques, such as baffle plates or channeling, to prolong oil retention in the tank and prevent air entrapment in the oil. Despite the implementation of these technologies, mobile systems retain an oil volume approximately 1 to 1.2 times the maximum attainable flow rate.
Simplifies hydraulic circuits
Hydraulic system elements interconnected by piping and hoses. If many high flow pumps are present, it is advisable to utilize a basic collector as illustrated. CVTANK included this system as a low-pressure accumulator. It can connect any point in the circuit. To avert oil stagnation in the CVTANK, leakage lines are routed towards the CVTANK, preferably via a cooler.
When an actuator or accumulator needs to change its internal volume, CVTANK compensates for this alteration by adjusting its stored volume to maintain circuit operation.
Eliminates hosing haywire
Every hydraulic pump specifies minimum pressure to work without problem for its inlet port. This specification value changes with pump manufacturer, and it increases with the increasing pump rotation speed.
To attain this pressure value, conventional tanks require wide-diameter hoses to connect the pumps. A standard pump on mobile machinery exceeds 60 cc and operates at up to 2000 RPM, requiring a minimum of 2-inch lines to provide the required intake pressures. The increased turning radii exceeding 150mm, along with a weight surpassing 2kg per meter and over 1kg per hose end, render these hoses a significant designing challenge alone.
CVTANK can connect any point on the return side of the hydraulic circuit with a traditional low pressure hydraulic hose probably not larger than the 1-inch. Suction hoses and their troubles can totally be eliminated.
Keeps pumps inlet pressurized.
Pumps need to suck hydraulic oil from atmospheric traditional hydraulic tanks. This limits pumps to reach their maximum allowable rpm speeds. With a CVTANK pumps pressurized according to their specification limits and can provide flow at their maximum capacity.
1. Oil:
CVTANK is exclusively compatible with mineral-based lubricants. Non-mineral-based oils require formal approval from HYDROBEY for usage in the product.
2. Pressure:
The product should not be used at pressure values higher than those specified in the HYDROBEY technical specifications or drains.
3. Temperature:
CVTANK operating ambient temperature is -40 °C – 100 °C and maximum oil temperature is 90 °C. For operating conditions outside these values, written approval from HYDROBEY is required.
4. Installation:
CVTANK fluctuates above and below its fill level to fulfill the hydraulic system's oil requirements. The product installation must ensure that no extraneous objects are present in the designated working area affected by this movement. No staff should be present in the CVTANK operational area while the system is functioning.
The assembly of threaded connection elements such as fittings, sensors, hoses, etc. to be installed on the CVTANK, must be made in accordance with the working procedures with hydraulic ports made of aluminum specified in their respective standards. Hose and cable connections shall not exert a stress on the product that exceeds the limits stated in the connection standards or in a direction other than the product's movement axis.
CV TANK FR series are not suitable for installation on vehicles where high vibration is expected (MIL-STD-810G etc.) without HYDROBEY approved accessories.
5. Alignment:
CVTANK must be positioned with the pipe section oriented perpendicular to the ground, ensuring the air intake point of the top cover is situated above.
The angular tolerance for the CVTANK's location relative to the ground is 5°. In installations over this threshold, the product's operational lifespan diminishes.
Approval from HYDROBEY is necessary for applications that do not adhere to the recommended installation conditions outlined here.
A pair of clamps according to DIN 3015 or a comparable specification must be used to install the CVTANK. HYDROBEY-approved mounting accessories or written authorization from HYDROBEY are necessary for installation options that differ from this.
|
CVTank |
Traditional Tank |
Breather |
None |
At least one |
Welding |
None |
Fully welded manufacturing with several different machining operations. |
Level measurement |
Pressure sensor (0-1 bar) or visual control. |
Float or level switch. It can’t give right information at the slope or during sloshing. |
Location on the machine |
Any location, In or above the vehicle. |
The closest point to the pump suction ports. |
Sloshing |
Not affected from sloshing. |
Detailed analysis and baffle plate design is required. |
Gradability |
Complies every grade requirement. |
It requires detailed analysis and specific structural design. |
Maintenance |
Visual checks. Traps particles out of suction ports with easy dump. |
Large flat surfaces, lot of stagnation areas, specific design effort to have access door for cleaning. |
Corrosion resistance |
Built with most used aluminum and stainless-steel parts already been proven on defense vehicles. |
Needs paint outside and coating inside. Interior surfaces exposed to atmosphere is prone to corrode. |
Leakage |
Hermetically sealed. If a leakage occurs in the system, it can be monitored via pressure sensor. It has designed to pass AECTP 400 (Edition 3) ANNEX B 401 vibration test. |
Welding seams, level glasses, breather etc. puts leakage risks. They mostly not tested against vibration tests. |
Change Procedure |
It can be changes without significant oil loss from the system as LRU. |
Probably whole powerpack needs to be uninstalled from the vehicle. |
Despite the implementation of all requisite safeguards and calculations done before to the operation, inadequate and timely maintenance may diminish the product's lifespan. Inspection, maintenance intervals, and replacement protocols should be established based on the criticality of system failure associated with the product's application.
1. Visual inspection:
CVTANK should be visually inspected as part of the daily maintenance routine. During visual inspection:
Rubber parts should be checked for cracks, discoloration, deformities, corrosive effects of foreign fluids, loose bolts, mounting bracket gaps.
2. Functional Test:
CVTANK should be tested monthly against its original desing condition. Best practice is to check pressure or height levels at any known state of the system.
If you experience any unusual vibrations, sounds, or pressures during tests, please contact HYDROBEY for troubleshooting assistance.
3. Maintenance and Suggested Replacement Periods:
The working lifetime of CVTANK is unrestricted when the maintenance and operational conditions needed by hydraulic systems are met. Operating conditions of the user will affect the maintenance intervals.
It is recommended that CVTANK be completely removed from the system at 5-year intervals and its internal parts be inspected and cleaned. Since the main material at the outside of the reservoir is rubber-based, if it has not been renewed during maintenance after 5 years, special attention should be paid to visual inspections. It is recommended that the sealing elements and the outer rubber lower part be renewed every 5 years.
No parts should be replaced on CVTANK. When maintenance is required, CVTANK should be completely removed from the hydraulic system and a spare one should be installed in the hydraulic system. The product that is removed after the replacement is used after the necessary inspections and provided that the maintenance is performed by HYDROBEY. For this, the product must be packaged in a clean plastic bag in a way that will not allow external contamination and will not suffer structural damage and must be delivered to HYDROBEY facilities. All sealing products and consumables of each product that comes for maintenance are renewed.